Budowa maszyn pneumatycznych opiera się na kilku kluczowych elementach, które współpracują ze sobą, aby osiągnąć zamierzony efekt. Podstawowym komponentem jest sprężarka, która odpowiada za wytwarzanie sprężonego powietrza. To właśnie sprężone powietrze jest nośnikiem energii w systemach pneumatycznych. Kolejnym istotnym elementem są siłowniki pneumatyczne, które przekształcają energię sprężonego powietrza w ruch mechaniczny. Siłowniki te mogą mieć różne kształty i rozmiary, co pozwala na ich zastosowanie w różnych aplikacjach. W budowie maszyn pneumatycznych nie można zapomnieć o zaworach, które kontrolują przepływ powietrza w systemie. Zawory te mogą być ręczne lub automatyczne, a ich odpowiedni dobór ma kluczowe znaczenie dla efektywności całego układu. Dodatkowo, w maszynach pneumatycznych często stosuje się filtry, które oczyszczają sprężone powietrze z zanieczyszczeń oraz osuszacze, które eliminują nadmiar wilgoci.
Jakie są zalety i wady maszyn pneumatycznych
Maszyny pneumatyczne mają wiele zalet, które sprawiają, że są one popularnym wyborem w różnych branżach przemysłowych. Jedną z głównych korzyści jest ich prostota konstrukcji, co przekłada się na łatwość obsługi oraz konserwacji. Dzięki zastosowaniu sprężonego powietrza jako medium roboczego, maszyny te są zazwyczaj lżejsze i bardziej kompaktowe niż ich hydrauliczne odpowiedniki. Ponadto, maszyny pneumatyczne charakteryzują się dużą szybkością działania oraz możliwością precyzyjnego sterowania ruchem. Warto również zauważyć, że sprężone powietrze jest bezpieczniejsze w użyciu niż oleje hydrauliczne, co zmniejsza ryzyko wycieków i zanieczyszczenia środowiska. Niemniej jednak maszyny pneumatyczne mają także swoje wady. Jednym z głównych ograniczeń jest konieczność dostarczania sprężonego powietrza do układu, co może wiązać się z dodatkowymi kosztami związanymi z eksploatacją sprężarek. Dodatkowo, efektywność energetyczna maszyn pneumatycznych może być niższa niż w przypadku innych systemów napędowych, takich jak hydraulika czy elektryka.
Jakie zastosowania mają maszyny pneumatyczne w przemyśle
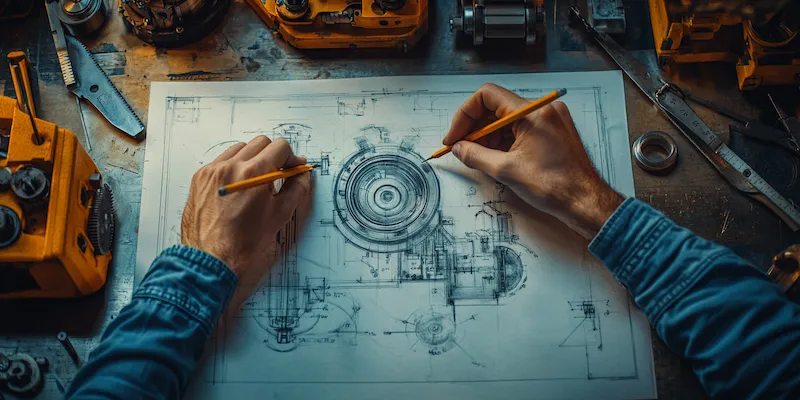
Maszyny pneumatyczne znajdują szerokie zastosowanie w różnych dziedzinach przemysłu ze względu na swoją wszechstronność i efektywność. W branży produkcyjnej często wykorzystuje się je do automatyzacji procesów montażowych oraz pakowania produktów. Siłowniki pneumatyczne umożliwiają szybkie i precyzyjne ruchy, co przyspiesza cały proces produkcji i zwiększa jego wydajność. W przemyśle motoryzacyjnym maszyny pneumatyczne są wykorzystywane do operacji takich jak malowanie karoserii czy montaż podzespołów. Dzięki swojej elastyczności mogą być łatwo dostosowywane do zmieniających się potrzeb produkcyjnych. W sektorze budowlanym maszyny pneumatyczne znajdują zastosowanie w narzędziach takich jak młoty udarowe czy wiertarki, które dzięki sprężonemu powietrzu działają z dużą mocą i efektywnością. Również w logistyce maszyny te odgrywają ważną rolę – systemy transportu pneumatycznego umożliwiają szybkie przesyłanie materiałów między różnymi strefami magazynowymi czy produkcyjnymi.
Jakie są nowoczesne technologie w budowie maszyn pneumatycznych
Nowoczesne technologie znacząco wpłynęły na rozwój budowy maszyn pneumatycznych, co pozwoliło na zwiększenie ich wydajności oraz funkcjonalności. W ostatnich latach nastąpił postęp w zakresie automatyzacji procesów związanych z obsługą maszyn pneumatycznych. Dzięki zastosowaniu zaawansowanych systemów sterowania możliwe jest precyzyjne zarządzanie pracą urządzeń oraz optymalizacja ich działania w czasie rzeczywistym. Wprowadzenie technologii Internetu Rzeczy (IoT) umożliwia monitorowanie stanu maszyn oraz przewidywanie potencjalnych awarii jeszcze przed ich wystąpieniem, co znacznie zwiększa niezawodność całego systemu. Dodatkowo nowoczesne materiały wykorzystywane w budowie komponentów maszyn pneumatycznych przyczyniają się do zmniejszenia ich masy oraz poprawy odporności na uszkodzenia mechaniczne i korozję. Innowacyjne rozwiązania takie jak inteligentne zawory czy siłowniki o zmiennej geometrii pozwalają na jeszcze lepsze dostosowanie pracy maszyn do specyficznych wymagań aplikacji przemysłowych.
Jakie są kluczowe różnice między systemami pneumatycznymi a hydraulicznymi
Wybór między systemami pneumatycznymi a hydraulicznymi jest często kluczowym zagadnieniem w projektowaniu maszyn i urządzeń przemysłowych. Oba systemy mają swoje unikalne cechy, które sprawiają, że są odpowiednie do różnych zastosowań. Systemy pneumatyczne wykorzystują sprężone powietrze jako medium robocze, co czyni je lżejszymi i bardziej elastycznymi w porównaniu do hydrauliki, która opiera się na cieczy pod ciśnieniem. Dzięki temu maszyny pneumatyczne są zazwyczaj prostsze w budowie i konserwacji. W przypadku hydrauliki mamy do czynienia z większą mocą i momentem obrotowym, co sprawia, że jest ona bardziej odpowiednia do cięższych prac wymagających dużych sił. Kolejną istotną różnicą jest wydajność energetyczna – systemy hydrauliczne mogą być bardziej efektywne w długotrwałych operacjach, podczas gdy pneumatyka lepiej sprawdza się w aplikacjach wymagających szybkich cykli pracy. Warto również zauważyć, że sprężone powietrze jest łatwiejsze do uzyskania i nie wymaga skomplikowanych układów filtracyjnych jak oleje hydrauliczne, co może wpływać na koszty eksploatacji.
Jakie są najczęstsze problemy w maszynach pneumatycznych
Maszyny pneumatyczne, mimo swoich licznych zalet, mogą napotykać różne problemy, które wpływają na ich wydajność i niezawodność. Jednym z najczęstszych problemów jest wyciek sprężonego powietrza, który może prowadzić do znacznych strat energii oraz obniżenia efektywności całego systemu. Wyciek ten może występować w wyniku uszkodzenia uszczelek lub połączeń, co wymaga regularnej konserwacji i inspekcji układu. Innym istotnym problemem jest zanieczyszczenie sprężonego powietrza, które może prowadzić do uszkodzenia komponentów oraz obniżenia jakości wykonywanych operacji. Dlatego ważne jest stosowanie odpowiednich filtrów oraz osuszaczy w celu zapewnienia czystości medium roboczego. Problemy z ciśnieniem roboczym również mogą występować, zwłaszcza jeśli sprężarka nie działa prawidłowo lub nie jest odpowiednio dobrana do wymagań systemu. Niewłaściwe ciśnienie może prowadzić do niewłaściwego działania siłowników oraz zaworów, co negatywnie wpływa na cały proces produkcji.
Jakie są trendy w rozwoju technologii maszyn pneumatycznych
Rozwój technologii maszyn pneumatycznych idzie w kierunku zwiększenia ich efektywności oraz integracji z nowoczesnymi systemami automatyki przemysłowej. Jednym z głównych trendów jest zastosowanie sztucznej inteligencji oraz uczenia maszynowego do optymalizacji procesów produkcyjnych. Dzięki analizie danych zbieranych z pracy maszyn możliwe jest przewidywanie awarii oraz dostosowywanie parametrów pracy do aktualnych potrzeb produkcji. Wprowadzenie rozwiązań opartych na chmurze pozwala na zdalne monitorowanie stanu maszyn oraz zarządzanie nimi z dowolnego miejsca na świecie. Kolejnym istotnym trendem jest miniaturyzacja komponentów pneumatycznych, co umożliwia ich zastosowanie w coraz bardziej kompaktowych rozwiązaniach inżynieryjnych. Zastosowanie nowych materiałów kompozytowych oraz technologii druku 3D przyczynia się do zwiększenia trwałości i odporności elementów maszyn pneumatycznych na uszkodzenia mechaniczne i korozję.
Jakie są koszty eksploatacji maszyn pneumatycznych
Koszty eksploatacji maszyn pneumatycznych mogą być różnorodne i zależą od wielu czynników, takich jak rodzaj zastosowania, intensywność pracy czy jakość używanych komponentów. Jednym z głównych kosztów związanych z eksploatacją tych maszyn jest energia potrzebna do wytworzenia sprężonego powietrza. Koszt ten może być znaczący, zwłaszcza jeśli sprężarka nie działa efektywnie lub jeśli występują straty związane z wyciekami powietrza. Regularna konserwacja oraz inspekcje układu są również niezbędne dla zapewnienia prawidłowego funkcjonowania maszyn i zapobiegania awariom, co wiąże się z dodatkowymi kosztami serwisowymi. Warto także uwzględnić wydatki na zakup części zamiennych oraz akcesoriów takich jak filtry czy osuszacze, które muszą być regularnie wymieniane dla utrzymania wysokiej jakości sprężonego powietrza. Koszty te można jednak częściowo zredukować poprzez inwestycje w nowoczesne technologie i komponenty o wysokiej wydajności energetycznej.
Jakie są przyszłościowe kierunki rozwoju budowy maszyn pneumatycznych
Przyszłość budowy maszyn pneumatycznych zapowiada się obiecująco dzięki ciągłemu postępowi technologicznemu oraz rosnącemu zainteresowaniu automatyzacją procesów przemysłowych. W miarę jak przemysł 4.0 staje się coraz bardziej powszechny, maszyny pneumatyczne będą musiały dostosować się do nowych standardów dotyczących inteligentnego zarządzania produkcją. Integracja z systemami IoT pozwoli na zbieranie danych o wydajności urządzeń oraz ich stanie technicznym w czasie rzeczywistym, co umożliwi szybsze podejmowanie decyzji dotyczących konserwacji czy optymalizacji procesów produkcyjnych. Rozwój technologii sztucznej inteligencji przyczyni się także do automatyzacji analizy danych oraz prognozowania awarii, co zwiększy niezawodność całego układu. W kontekście ochrony środowiska rośnie również znaczenie efektywności energetycznej maszyn pneumatycznych – producenci będą dążyć do tworzenia rozwiązań minimalizujących zużycie energii oraz redukujących emisję hałasu związane z pracą tych urządzeń. Nowe materiały kompozytowe oraz technologie produkcji będą miały kluczowe znaczenie dla dalszego rozwoju komponentów pneumatycznych o lepszych parametrach wytrzymałościowych i mniejszych gabarytach.