Destylator przemysłowy to urządzenie, które odgrywa kluczową rolę w procesach separacji i oczyszczania cieczy. Jego działanie opiera się na różnicy temperatur wrzenia substancji, co pozwala na oddzielenie składników mieszaniny. W przemyśle chemicznym, petrochemicznym oraz spożywczym destylacja jest niezbędnym procesem, który umożliwia uzyskiwanie czystych substancji oraz koncentratów. W przypadku destylacji prostej, ciecz jest podgrzewana do momentu, gdy jeden z jej składników zaczyna wrzeć. Para powstała w wyniku wrzenia jest następnie schładzana i skraplana, co prowadzi do uzyskania cieczy o wyższej czystości. W bardziej zaawansowanych systemach, takich jak kolumny destylacyjne, proces ten jest znacznie bardziej skomplikowany i efektywny. Kolumny te są wyposażone w różne elementy, takie jak tray’e czy packingi, które zwiększają powierzchnię kontaktu między parą a cieczą, co prowadzi do lepszej separacji składników.
Jakie są zastosowania destylatorów przemysłowych w różnych branżach
Destylatory przemysłowe znajdują szerokie zastosowanie w wielu branżach, co czyni je niezwykle wszechstronnymi urządzeniami. W przemyśle chemicznym służą do produkcji różnych substancji chemicznych, takich jak rozpuszczalniki czy kwasy. W branży petrochemicznej destylacja jest kluczowym procesem przy produkcji paliw, gdzie surowa ropa naftowa jest poddawana destylacji frakcyjnej w celu uzyskania benzyny, oleju napędowego oraz innych produktów naftowych. W przemyśle spożywczym destylatory są wykorzystywane do produkcji alkoholi oraz ekstraktów smakowych. Na przykład w produkcji whisky czy wina proces destylacji ma ogromne znaczenie dla uzyskania odpowiednich walorów smakowych i aromatycznych. Ponadto destylatory znajdują zastosowanie w laboratoriach badawczych do oczyszczania substancji chemicznych oraz w medycynie do produkcji leków.
Jakie są kluczowe elementy konstrukcyjne destylatora przemysłowego
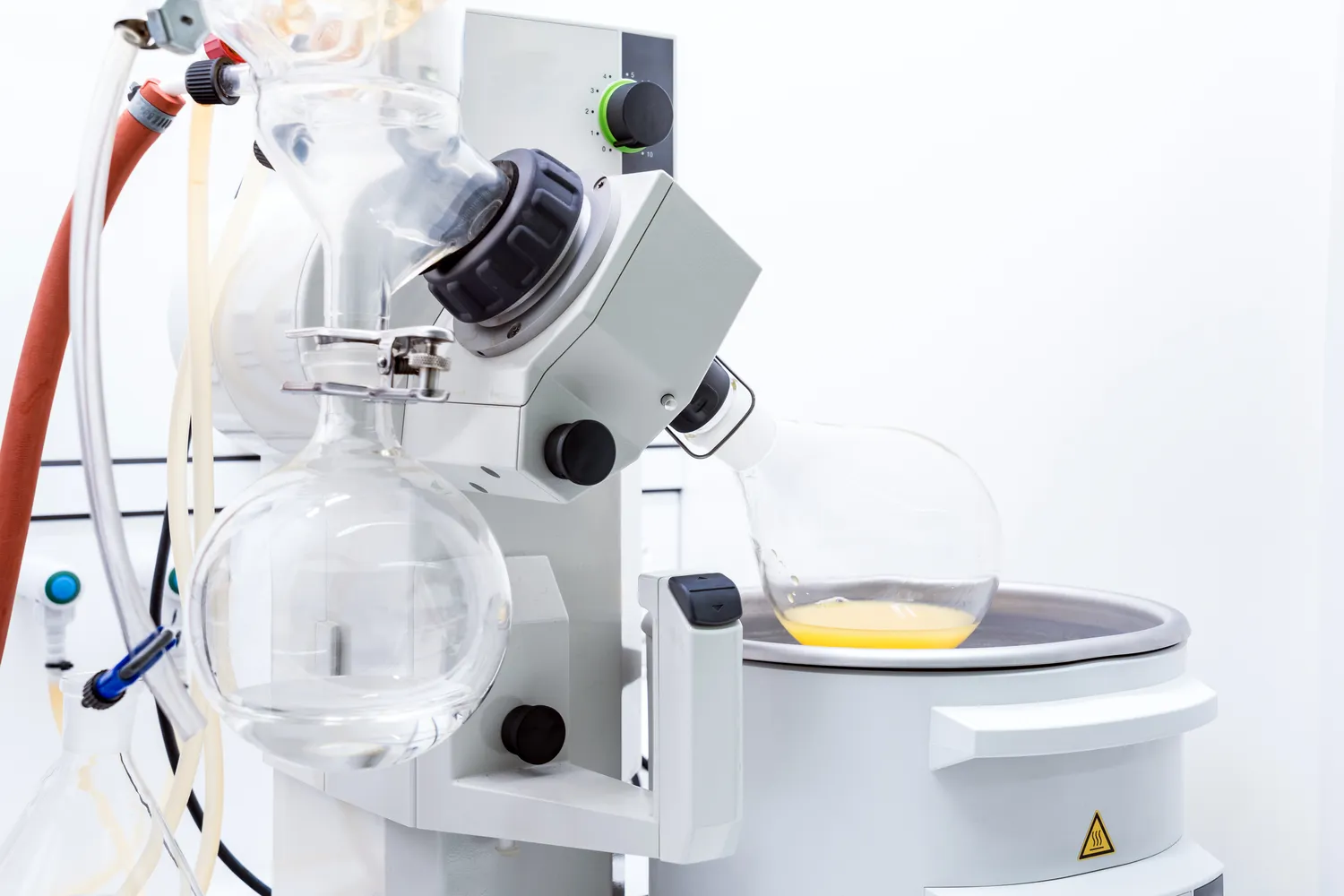
Konstrukcja destylatora przemysłowego opiera się na kilku kluczowych elementach, które zapewniają jego efektywność i funkcjonalność. Podstawowym elementem jest zbiornik na ciecz, który jest podgrzewany do momentu wrzenia. Obok zbiornika znajduje się system grzewczy, który może być oparty na różnych źródłach energii, takich jak para wodna czy elektryczność. Kolejnym istotnym elementem jest kolumna destylacyjna, która pełni rolę separatora składników. Wewnątrz kolumny znajdują się tray’e lub packingi, które zwiększają powierzchnię kontaktu między parą a cieczą, co pozwala na skuteczniejszą separację substancji. Po przejściu przez kolumnę para trafia do skraplacza, gdzie zostaje schłodzona i skroplona z powrotem do postaci cieczy. Oprócz tych podstawowych komponentów destylatory mogą być wyposażone w różne systemy monitorujące oraz kontrolujące proces, co pozwala na optymalizację pracy urządzenia oraz zwiększenie jego wydajności.
Jakie są najnowsze technologie w dziedzinie destylacji przemysłowej
W ostatnich latach technologia destylacji przemysłowej uległa znacznemu rozwojowi dzięki innowacjom inżynieryjnym oraz nowym materiałom. Jednym z najważniejszych trendów jest automatyzacja procesów destylacyjnych, która pozwala na precyzyjne monitorowanie i kontrolowanie parametrów pracy urządzenia. Dzięki zastosowaniu nowoczesnych czujników oraz systemów informatycznych możliwe jest zdalne zarządzanie procesem oraz szybkie reagowanie na zmiany warunków pracy. Kolejnym istotnym kierunkiem rozwoju są technologie oszczędzające energię, takie jak rekuperacja ciepła czy wykorzystanie energii słonecznej do podgrzewania cieczy. Te innowacje przyczyniają się do zmniejszenia kosztów operacyjnych oraz ograniczenia wpływu na środowisko naturalne. Również materiały używane do budowy destylatorów uległy zmianie – nowoczesne stopy metali oraz tworzywa sztuczne charakteryzują się lepszą odpornością na korozję i wysokie temperatury, co zwiększa trwałość urządzeń.
Jakie są różnice między destylacją prostą a frakcyjną w przemyśle
Destylacja prosta i frakcyjna to dwa podstawowe typy procesów destylacyjnych, które różnią się zarówno sposobem działania, jak i zastosowaniem. Destylacja prosta jest najprostszą formą tego procesu, polegającą na podgrzewaniu cieczy do momentu jej wrzenia, a następnie skraplaniu powstałej pary. Jest to metoda stosunkowo łatwa do zrealizowania i wykorzystywana głównie w przypadku substancji o znacznej różnicy temperatur wrzenia. Przykładem może być oczyszczanie wody z soli czy innych zanieczyszczeń. W przeciwieństwie do tego, destylacja frakcyjna jest bardziej skomplikowanym procesem, który pozwala na separację mieszanin z wieloma składnikami o zbliżonych temperaturach wrzenia. W tym przypadku używa się kolumny destylacyjnej, która umożliwia wielokrotne skraplanie i odparowywanie składników, co prowadzi do ich lepszej separacji. Destylacja frakcyjna jest szeroko stosowana w przemyśle petrochemicznym do produkcji paliw oraz w przemyśle chemicznym do uzyskiwania czystych substancji chemicznych.
Jakie są kluczowe czynniki wpływające na efektywność destylacji przemysłowej
Efektywność procesu destylacji przemysłowej jest uzależniona od wielu czynników, które należy uwzględnić podczas projektowania i eksploatacji destylatorów. Jednym z najważniejszych aspektów jest temperatura, która ma kluczowe znaczenie dla procesu wrzenia cieczy. Odpowiednie ustawienie temperatury pozwala na optymalne oddzielenie składników mieszaniny. Kolejnym czynnikiem jest ciśnienie, które również wpływa na temperaturę wrzenia substancji. W niektórych przypadkach stosuje się destylację pod zmniejszonym ciśnieniem, co pozwala na obniżenie temperatury wrzenia i minimalizację degradacji termicznej wrażliwych składników. Inne istotne elementy to czas kontaktu pary z cieczą oraz powierzchnia wymiany ciepła w kolumnie destylacyjnej. Im dłużej para ma kontakt z cieczą, tym lepsza separacja składników jest możliwa. Dodatkowo, jakość materiałów użytych do budowy destylatora oraz ich odporność na korozję mają wpływ na trwałość i efektywność urządzenia.
Jakie są wyzwania związane z eksploatacją destylatorów przemysłowych
Eksploatacja destylatorów przemysłowych wiąże się z szeregiem wyzwań, które mogą wpływać na efektywność i bezpieczeństwo pracy tych urządzeń. Jednym z głównych problemów jest konieczność regularnego utrzymania i konserwacji sprzętu, aby zapobiec awariom oraz zapewnić ciągłość produkcji. Z biegiem czasu mogą występować osady oraz zanieczyszczenia wewnątrz kolumny destylacyjnej, co prowadzi do spadku wydajności procesu. Dlatego regularne czyszczenie i inspekcje są niezbędne dla zachowania wysokiej jakości produktów końcowych. Innym wyzwaniem jest zarządzanie energią potrzebną do podgrzewania cieczy – wysokie koszty energii mogą znacząco wpłynąć na rentowność procesu. W związku z tym wiele zakładów stara się wdrażać rozwiązania oszczędzające energię oraz technologie odzysku ciepła. Ponadto, bezpieczeństwo pracy jest kluczowym aspektem eksploatacji destylatorów – wysokie temperatury oraz ciśnienia mogą stwarzać zagrożenie dla pracowników i środowiska.
Jakie są najczęstsze błędy przy obsłudze destylatorów przemysłowych
Obsługa destylatorów przemysłowych wymaga dużej precyzji oraz znajomości zasad działania tych urządzeń, jednak często zdarzają się błędy, które mogą prowadzić do obniżenia efektywności procesu lub nawet awarii sprzętu. Jednym z najczęstszych błędów jest niewłaściwe ustawienie parametrów pracy, takich jak temperatura czy ciśnienie. Niezgodności te mogą prowadzić do niepełnej separacji składników lub ich degradacji. Kolejnym problemem jest brak regularnej konserwacji urządzeń – zaniedbania w tej kwestii mogą skutkować powstawaniem osadów wewnątrz kolumny czy uszkodzeniami elementów grzewczych. Również niewłaściwe zarządzanie surowcami może prowadzić do problemów z jakością produktu końcowego – nieodpowiednie przygotowanie mieszanin może skutkować niepożądanymi reakcjami chemicznymi podczas procesu destylacji. Ważne jest również przestrzeganie procedur bezpieczeństwa – lekceważenie zasad BHP może prowadzić do poważnych wypadków w miejscu pracy.
Jakie są przyszłe kierunki rozwoju technologii destylacyjnych
Przyszłość technologii destylacyjnych zapowiada się obiecująco dzięki ciągłemu postępowi technologicznemu oraz rosnącym wymaganiom rynku dotyczących efektywności energetycznej i ochrony środowiska. Jednym z głównych kierunków rozwoju są technologie oparte na sztucznej inteligencji i automatyzacji procesów, które umożliwiają optymalizację parametrów pracy w czasie rzeczywistym oraz przewidywanie potencjalnych awarii przed ich wystąpieniem. Dzięki zastosowaniu zaawansowanych algorytmów możliwe będzie zwiększenie wydajności procesów oraz redukcja kosztów operacyjnych. Kolejnym istotnym trendem jest rozwój materiałów o wysokiej odporności na korozję oraz ekstremalne warunki temperaturowe, co przyczyni się do zwiększenia trwałości urządzeń i obniżenia kosztów ich eksploatacji. W kontekście ochrony środowiska rośnie zainteresowanie technologiami zielonej chemii, które minimalizują negatywny wpływ procesów przemysłowych na otoczenie poprzez zmniejszenie zużycia energii oraz emisji gazów cieplarnianych.
Jakie są różnice między małymi a dużymi destylatorami przemysłowymi
Różnice między małymi a dużymi destylatorami przemysłowymi dotyczą przede wszystkim skali produkcji, konstrukcji oraz zastosowania tych urządzeń. Małe destylatory często znajdują zastosowanie w laboratoriach badawczych lub w małych zakładach produkcyjnych, gdzie wymagane są niewielkie ilości substancji chemicznych lub alkoholi. Charakteryzują się one prostszą konstrukcją, mniejszymi wymiarami oraz niższymi kosztami zakupu i eksploatacji. Z kolei duże destylatory przemysłowe są przeznaczone do masowej produkcji i charakteryzują się bardziej skomplikowaną budową oraz większą wydajnością. W przypadku dużych instalacji często wykorzystuje się zaawansowane technologie takie jak kolumny wielofrakcyjne czy systemy automatyzacji procesów, co pozwala na osiąganie wysokiej jakości produktów przy jednoczesnym obniżeniu kosztów operacyjnych.